Why Custom Lithium Batteries Are in High Demand
In today’s rapidly evolving technological landscape, lithium batteries are indispensable to modern life. Powering everything from smartphones and laptops to eco-friendly electric vehicles and drones for outdoor exploration, lithium batteries offer high energy density, long cycle life, and low self-discharge rates for reliable performance. However, as industries innovate and niche markets expand, standardized lithium batteries often fall short of meeting specialized application needs. For instance, scientific equipment in polar or high-altitude regions requires batteries with exceptional low-temperature performance to operate in extreme cold.
Medical implantable devices demand ultra-compact lithium batteries with superior stability to ensure patient safety. Industrial automation systems require batteries with precise charge-discharge rates and stable voltage platforms to meet stringent operational standards. In response, the custom lithium battery industry has surged, addressing these unique demands. Custom solutions are tailored to specific devices and applications, covering cell selection, battery management system (BMS) design, physical encapsulation, and performance specifications.
These bespoke designs ensure compatibility with diverse and complex operating conditions. A key concern for those seeking customization is cost. Custom lithium battery pricing is shaped by multiple factors, which we explore below.
Cost Breakdown of Custom Lithium Batteries
1. Battery Cells: The Primary Cost Driver
The battery cell, the core of any lithium battery, accounts for 40% to 60% of the total cost. Cells vary by cathode material, leading to significant differences in performance and price. For example, lithium cobalt oxide (LCO) cells, with high energy density, deliver robust power but are expensive, making them ideal for premium consumer electronics like smartphones and tablets. Lithium iron phosphate (LFP) cells provide enhanced safety, long cycle life, and cost-effectiveness, favored in electric vehicles and energy storage systems. Nickel manganese cobalt (NMC) cells balance energy density, safety, and cost through optimized material ratios, widely used in power tools, low-speed EVs, and select passenger vehicles.
Brand reputation significantly influences cell costs. Leading global brands, leveraging advanced technology, stringent quality controls, and strong market credibility, charge a premium. Cells from manufacturers like Panasonic, Samsung, and LG dominate high-end electronics and EV markets, typically priced 20% to 50% higher than domestic alternatives. However, domestic leaders like CATL, BYD, and EVE Energy have bolstered R&D, enhancing quality and competitiveness, gaining global recognition. Cell capacity directly impacts cost. Higher capacity requires more active materials, increasing production expenses. For instance, a 2000mAh 18650 cell may cost $0.40 to $0.70, while a 3000mAh cell ranges from $1.10 to $1.70. In large-capacity custom batteries, such as EV power packs, cell costs dominate, heavily influencing the final price.
2. Battery Management System (BMS): Intelligent Oversight
The battery management system (BMS) serves as the “intelligent core” of a lithium battery, ensuring safety, monitoring performance, and optimizing longevity. It collects real-time data on voltage, current, and temperature, using sophisticated algorithms to calculate state of charge (SOC) and state of health (SOH). This enables precise control of charging and discharging, preventing overcharging, over-discharging, or overheating, thus extending battery life.
BMS complexity and performance requirements directly affect costs. For small-scale applications like power banks or LED flashlights, a basic BMS with overcharge and over-discharge protection is sufficient, comprising 5% to 10% of the total cost. In contrast, high-performance systems in EVs or energy storage require advanced BMS with superior reliability.
These manage thousands of cells, ensuring voltage and temperature consistency, and support high-speed communication, remote monitoring, fault diagnostics, and predictive alerts. Such BMS incorporate high-precision sensors, powerful microcontrollers, and complex circuits, driving up R&D and production costs. In these cases, BMS costs can account for 15% to 25% of the total. For example, a high-end EV BMS may cost thousands or tens of thousands of dollars, significantly impacting customization pricing.
3. Casing and Encapsulation: Protective Design
While seemingly secondary, casing and encapsulation substantially influence customization costs. Casing materials vary, each with distinct benefits. Plastic casings, valued for low cost, light weight, and ease of molding, are common in consumer electronics. Aluminum alloy casings offer excellent heat dissipation, durability, and an appealing aesthetic, suitable for power tools and laptop batteries. Stainless steel casings, with superior corrosion resistance and strength, excel in demanding industrial or military applications.
Aluminum-plastic film, used in pouch cells, is lightweight and flexible, enhancing energy density and gaining traction in high-end electronics and select EV batteries. Casing design and encapsulation processes also drive costs. Custom shapes, sizes, colors, or branded logos often require specialized molds, costing thousands to tens of thousands of dollars.
Encapsulation techniques vary in expense. Simple injection molding is cost-effective for mass-produced casings. High-precision methods like laser welding or waterproof sealing enhance protection and reliability but increase costs. In waterproof, dustproof, or explosion-proof battery projects, casing and encapsulation costs may represent 10% to 15% of the total.
4. Custom Design and R&D: Tailored Solutions
The premium cost of custom lithium batteries largely stems from specialized design and R&D efforts. When clients request unique dimensions or shapes, manufacturers must redesign battery structures to fit specific device spaces. This involves simulation analysis, prototype development, and iterative testing, demanding significant time, labor, and resources. For example, a battery for a non-standard wearable device may need to be curved or ultra-thin, requiring innovative cell selection, arrangement, and casing molds. Such efforts can increase R&D costs by 20% to 50% compared to standard batteries.
Enhanced performance demands—such as faster charging, low-temperature resilience, or extended cycle life—require targeted R&D in materials, electrodes, and electrolytes. These efforts involve skilled professionals, advanced equipment, and extensive testing, further elevating costs. For instance, improving low-temperature performance may require specialized electrolytes and optimized electrode structures, taking months or years to ensure functionality at -20°C or below. These R&D investments are reflected in the final customization cost.
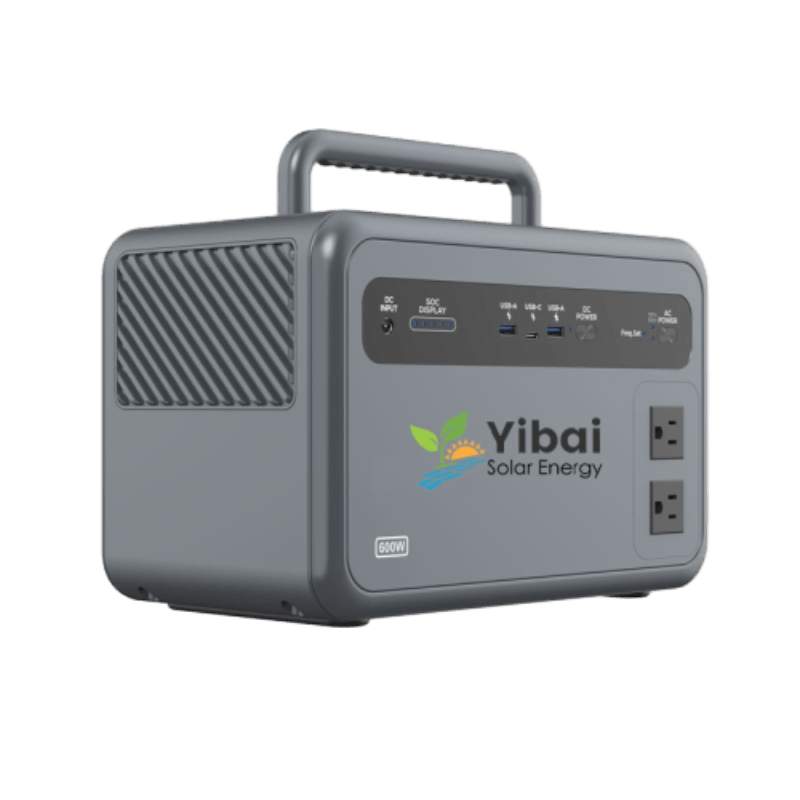
Key Factors Influencing Custom Battery Costs
1. Battery Specifications
Specifications like voltage, capacity, and charge-discharge rates significantly impact costs. Devices require specific voltages for stable operation. Consumer electronics typically use single 3.7V or 3.8V cells, while e-bikes and low-speed EVs use 36V or 48V packs with serial cell configurations. Higher voltages require more cells and advanced voltage management, increasing complexity and cost. A 72V battery for an electric motorcycle, compared to a 48V pack, demands additional cells and precise balancing circuits, significantly raising costs.
Capacity correlates closely with cost, as noted in the cell section. Large-scale energy storage systems, measured in megawatt-hours (MWh), require thousands of high-capacity cells, making capacity a major cost driver. Applications like marine propulsion or off-grid power in remote areas demand large-capacity batteries, further increasing costs.
Charge-discharge rates, critical for high-power applications, reflect a battery’s ability to handle rapid charging or discharging. Power tools and fast-charging EVs require high-rate batteries, posing challenges for cell materials, design, and BMS. High-conductivity materials like high-nickel NMC are costly, and designs must optimize electrode porosity and electrolyte performance. The BMS needs rapid response and precise control to prevent overheating or lithium plating. A racecar battery with 10C+ discharge rates for rapid acceleration costs several times more than standard EV batteries with 1C to 3C rates.
2. Application-Specific Demands
Industries impose varied performance and reliability requirements, profoundly affecting costs. In EVs, batteries require high energy density for extended range, robust charge-discharge rates for fast charging, and stability across diverse conditions to reduce “range anxiety.” Premium cells like high-nickel NMC or LFP “blade batteries,” paired with advanced BMS featuring thermal management and diagnostics, undergo rigorous safety tests (e.g., needle penetration, fire exposure). These demands and complex testing drive EV battery costs to tens of thousands of dollars or more.
In energy storage, batteries prioritize cycle life, efficiency, and cost-effectiveness for grid balancing or backup power. Daily cycling in solar or wind projects requires durable LFP cells and optimized BMS to minimize degradation, with large-scale (hundreds of MWh) projects costing tens or hundreds of millions. Consumer electronics demand compact, high-density batteries with custom designs. Smartphones use stacking techniques for space efficiency and aesthetic integration, with high-end batteries costing $5 to $15 despite smaller capacities.
3. Order Volume
Order volume significantly influences costs. Bulk orders leverage economies of scale, reducing costs through better material pricing. Small-batch 18650 cells cost $0.70 to $1.10, while millions of units may drop to $0.40 to $0.70. Large orders optimize production, spreading fixed costs (e.g., equipment, rent) and improving efficiency. A power tool battery supplier with hundreds of thousands of annual orders boosted efficiency by 30% and cut defects below 1%, lowering costs. Small batches, like those for research or medical devices, face higher unit costs due to limited scale and extra R&D, often costing several times more.
4. Brand and Quality Standards
Brand and quality standards significantly affect pricing. Global leaders like Panasonic, Samsung SDI, and LG Chem, with patented technologies (e.g., Panasonic’s 21700 cells), charge 20% to 50% premiums for superior materials, automated production, and comprehensive support. High-reliability applications like aerospace or rail require certifications (e.g., FAA, EASA), using specialized materials and redundant designs, increasing costs several-fold.
Typical Price Ranges for Custom Lithium Batteries
1. Consumer Electronics
Smartwatches and earbuds require low-capacity batteries with strict size and safety specs. Smartwatch batteries (100-500mAh) cost $0.70 to $2.10 for standard models, or $2.80 to $7.00 for high-density or fast-charging units. Earbud batteries (20-200mAh) range from $0.30 to $0.70 for basic models and $1.10 to $2.10 for premium units.
2. Power Tools
Power tools need high-rate batteries (12V, 18V, 21V; 1-5Ah). A mid-tier 18V, 2Ah pack costs $11 to $50, while premium units with advanced BMS cost $28 to $50. Industrial high-rate batteries may exceed $140.
3. EVs and Energy Storage
E-bike batteries (36V, 10Ah) cost $70 to $110; 48V, 20Ah units cost $170 to $280. Low-speed EV packs (60V, 72V; 100-200Ah) range from $420 to $1,100. Home energy storage (5-10kWh) costs $1,400 to $4,200; commercial systems (100-500kWh) reach tens or hundreds of thousands.
How to Optimize Custom Battery Costs
1. Define Precise Requirements
Analyze operational needs to specify battery requirements accurately. For standard devices like robotic vacuums, avoid over-specifying energy density or cycle life. For extreme conditions, prioritize resilience while simplifying non-critical features. A security camera’s battery was adjusted from 5-year operation to 4-6 hour backup, cutting costs by 30%.
2. Evaluate Multiple Suppliers
Solicit quotes from various suppliers, comparing cost breakdowns and reputations. An e-bike battery project chose a mid-tier supplier, saving 20% over a premium option while ensuring quality.
3. Leverage Partnerships and Bulk Orders
Long-term supplier partnerships or bulk orders reduce costs. A smart home device maker’s three-year deal yielded 5%, 8%, and 10% discounts over time, enhancing competitiveness. Joint procurement with similar businesses can also lower costs.
Future Outlook for Custom Lithium Batteries
The custom lithium battery market is poised for significant growth. Advancements in energy density and cost reductions will expand applications. In EVs, custom batteries will drive competitive, consumer-focused models, boosting adoption. In energy storage, tailored systems will enhance grid stability and sustainability. In consumer electronics, demand for compact, high-performance batteries will rise with smart device trends. Intensifying competition will require increased R&D, cost control, and superior service. Fueled by innovation and demand, the industry will power global energy and tech advancements, ushering in a dynamic future.